Things to consider when laying a new timber floor
posted: 03/Aug/2015
Below is a photo of a new timber floor laid in a renovation of an existing house. The floor had ‘tented’ in numerous locations. This reason for undesirable situation could be attributed to the high sub-floor moisture conditions that exist due to proximity to ground, inadequate sub-floor ventilation (and possibly poor drainage) and not making allowance for or addressing the existing conditions before laying the new floor.
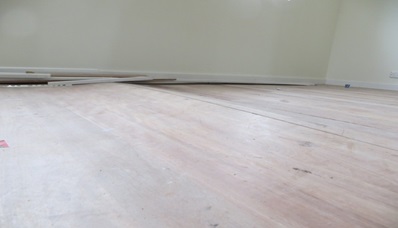
Not the result the owner was looking for
T&G flooring is typically supplied at 10 to 12% moisture content (MC) and the sub-floor MC in the house inspected was around 15% so the flooring has expanded around 15mm per metre width of floor since laying. This magnitude of movement is always going to result in dramatic results.
The message is clear, make sure that before laying floors in a renovation (even if the old floor to be removed looks OK) undertake a detailed investigation of the environmental moisture conditions including oven dry testing of existing sub-floor or flooring timbers to get an accurate gauge of moisture content in sub-floor spaces. This recommendation is also applicable for any new T&G floor as well. Refer to Timber Queensland's Technical Data sheets that give detailed guidance on pre-installation recommendations. You can obtain these data sheets from your local Accredited Queensland Timber Merchant.
Note: Older T&G hardwood floors were probably laid at higher MC than what is usual today.
Previous Articles
Build them up, build them up, build them higher!
The prevalence of non-conforming building products is a major concern for the Queensland building and construction industry with widespread use putting homeowners at risk.
For the past few years leading-edge architects, engineers and builders have been experimenting with and talking up the use of Cross Laminated Timber (CLT) as the building material of the future.